Bill and Mary Elder’s desire to build a log home percolated over a number of years. “When our children were young,” says Mary, “we owned a small log cabin about a half hour away from our Fredericktown home. It was perfect for weekend getaways and gave Bill some necessary down time from his busy medical practice.” As the Elder children grew up and became more involved in school activities, cabin time was less frequent. “We were reluctant to sell it,” says Bill, “so we rented it out for a while, then eventually we decided to put the cabin on the market, but our affection for log homes was firmly established in our minds and hearts and never diminished.”
Fast-forward the child-rearing years; grandchildren began to appear on the scene for Bill and Mary and thoughts of retirement surfaced more frequently in their conversations. “We began subscribing to magazines about log homes,” says Mary, “thinking a retirement home in a peaceful forest setting would be ideal for us.” The couple also began touring log homes whenever possible to scope out design ideas for their own place.
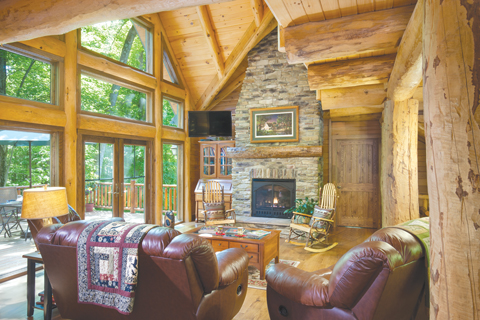
Bill had grown up on a farm with forestland and, in addition to enjoying being in the woods, he loved to cut it. “My husband has a lot of construction experience,” tells Mary. “He loves to build with wood. He remodeled and built several room additions on our home and his office. He’s a natural at the art and craft of design and construction.” Having determined he and Mary were going to build a log home at some point, Bill began harvesting various wood species—oak, walnut, cherry and ash—that could eventually be used in their home’s construction.
The couple first discovered their retirement property when Bill was participating in a church woodcutting service project. It had beautiful, giant trees and was near a large pond. A private northeast corner of the lot, with a gentle slope, was an ideal spot for a walkout basement. Bill says, “I knew in an instant the property was perfect for our dream log home. A few years later our friends, and future neighbors, told us when the parcel came up for sale.” The property was close to family, friends, and work, not far from town but away from the main road. Deer and turkey were the closest neighbors. The Elders considered the location ideal for their lifestyle, as they were both currently working but looking forward to an active retirement in the Fredericktown community they had been born and raised in. They purchased the land, began clearing it for a building site, and ramped up their log home pursuit.
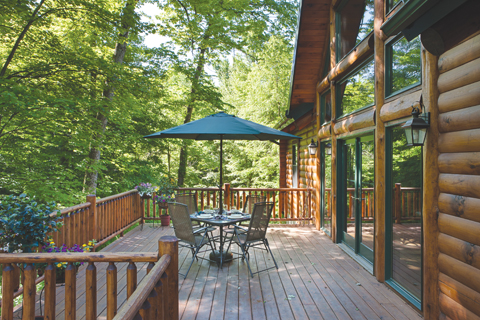
“We were wide open to design ideas, kind of a blank canvas,” says Mary, “so we sought out every opportunity to get inspiration for our house. We went to a log home trade show in Columbus where there were numerous log and timber companies exhibiting their products and explaining their packages. Then we saw an ad in a local paper for Hochstetler Milling’s “Log Cabin Days” and we attended.”
Each year Hochstetler Milling, an Amish firm founded by Levi Hochstetler in 1986, hosts a weekend filled with educational seminars and fun family activities at their Loudonville, Ohio, headquarters. Workshops cover numerous topics, including how to find and purchase land, log home financing, design and construction of log homes, and maintenance to be expected once the home is completed.
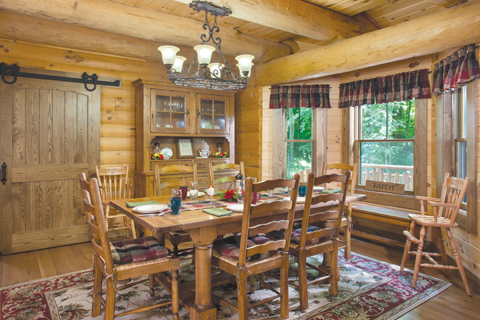
“At the event,” tells Mary, “Bill soon discovered that several of the Hochstetler clan were patients in his office!” Levi runs the large log milling operation. Mahlon, of Buckeye Builders, serves as a general contractor for log home construction, and Norman is responsible for the steel, standing-seam roofs. Their close friends poured concrete foundations. All had impeccable reputations. The Elders made their decision to contract with Hochstetler Milling for their dream log home.
As the saying goes, “good things take time,” and such was the case for the Elders. “It was about three years,” says Bill, “from the time we began clearing the property to breaking ground for the house. Developing the plans took about six months.” Bill drew some rough sketches and a friend drafted them on blueprint paper. Bill took the blueprints to Hochstetler Milling, who modified them. “The plans were redrawn and modified again, then again,” recalls Mary. “This was definitely a custom design. I think we ultimately built from the sixth set of blueprints.”
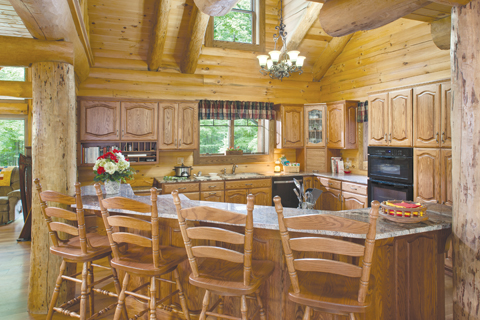
Bill and the Hochstetler team worked together closely throughout the project. “My husband would be on the job site before or after his day job, and on some days during his lunch hour,” elaborates Mary. “There were many things about the house plans that we had discussed and agreed upon together, but the construction part was definitely his baby.”
Hochstetler suggested subcontractors for the foundation, outer shell of the home, main floor fireplace, steel roofing, and the log stairs. Bill, a local Fredericktown native and family physician, had a substantial network of skillful patients and friends to use for the home’s excavation, basement cement work, electric, and plumbing.
Designed for retirement living, Bill and Mary wanted to be able to live on one floor of the house. They incorporated principles of Universal Design with easy access from garage to house, an open living space and wide doors and corridors, all wheelchair friendly. “This wide open great room design also allowed ample space for my baby grand piano and harp,” says Mary. “Even the loft, which we have set up for the grandkids to play in, is open to the areas below so our family can be in different areas of the house and still feel a part of the group.” The couple incorporated convenient laundry appliances into their main floor master bedroom closet.
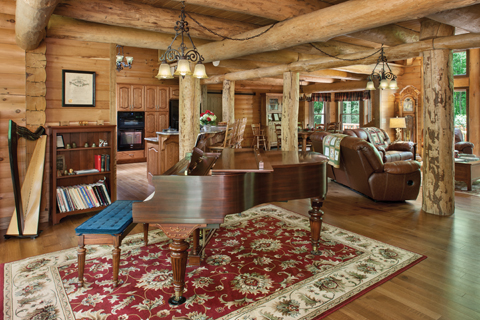
The Elders consider the most notable feature of their home to be the huge cherry and ash logs incorporated into the structure. The ash trees, used as beams, are 15 to 18 inches in diameter and span 20 feet. Wide-diameter cherry posts rise from floor to cathedral ceilings. “Bill harvested all of these trees, which were standing dead or blighted,” says Mary. “During one of our meetings with Levi Hochstetler he told us, ‘You have some pretty big sticks out there.’ We decided on the spot to name our home ‘Big Stix.’”
Interior walls and many of the doors are solid milled cherry and walnut, also harvested by Bill and a friend. Bill hauled the logs to an Amish sawmill for lumber. He stored the boards for six months to a year, then had them kiln dried for longer term storage prior to the start of construction.
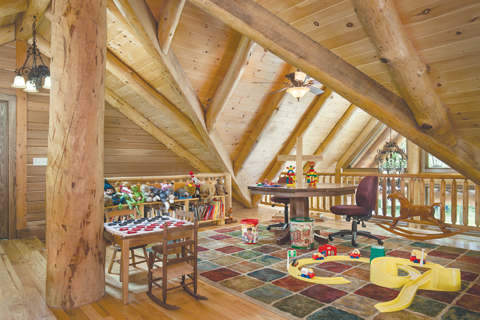
Exterior log walls are Hochstetler’s double-round design, with saddlenotch joints. “We think they look like Lincoln logs,” says Mary, “and provide a lot of character inside and out. We chose a fairly light stain from the range of colors that Hochstetler offered to us.” Hochstetler provided the milled exterior wall logs, rafters, ceiling sheathing, oak flooring, and Andersen windows and exterior doors. The Elders chose to upgrade from 8-inch to 10-inch logs, taking into consideration the scale of the interior timbers that Bill had provided for the house. The couple also upgraded their wood flooring from standard oak to quarter-sawn, which imparts a more rustic look to the floor.
“We designed our room layouts partially around the furniture we already had,” says Mary, “including the baby grand. As we needed and purchased furniture through the years, we acquired pieces that would someday fit nicely into a log home!” The Elders purchased new floor rugs, lighting fixtures, and granite countertops for the log house. Their custom kitchen cabinets, built by the Amish, were installed with the help of multiple friends.
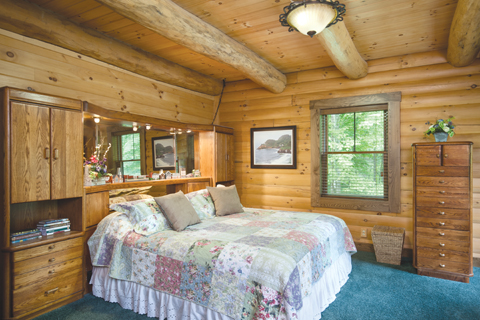
Bill and Mary say that to bring a custom log home dream to reality you have to do a lot of homework and then be ready to pitch in with the real work or oversee it. Bill cut in the five-foot-deep, 600-foot-long trench for the electric and phone with the help of a friend who owned a backhoe. He laid out the driveway with an excavator, and a patient delivered the limestone to cover it. He assisted with moving tons of dirt for the front yard fill, then graded the topsoil and planted more than 700 daffodils.
“Big Stix is truly a labor of love,” declares Mary. “We dreamed it together and saw it through to completion. To make it work, you need to work closely with subcontractors and listen to their advice. It’s also smart to talk to homeowners and experts who have gone through the process, to hear about their experiences and get their opinions. Plan, think, and take your time until you are sure of what you want.” And it doesn’t hurt to have a husband who loves to cut wood.